Kaizen
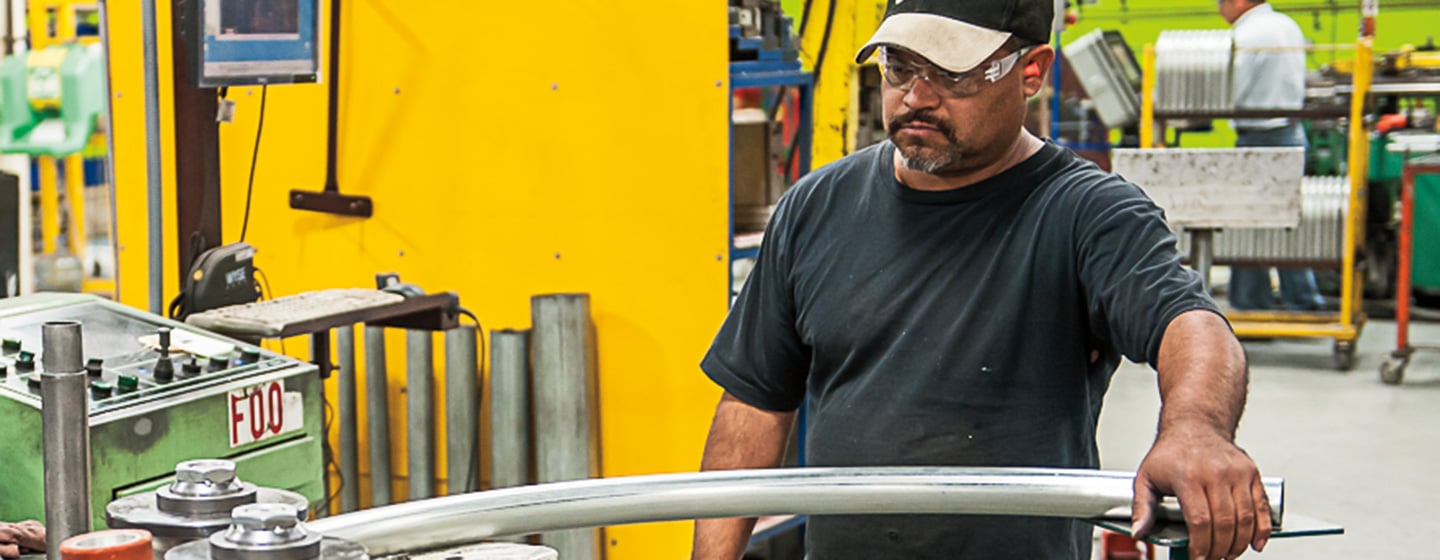
Lean Manufacturing
During this process, we studied lean manufacturing techniques. What would happen if we started manufacturing to order and stopped picking our products from an enormous inventory of parts?
The kaizen approach to manufacturing allowed us to enter uncharted territory and carried us from delivering goods to customers in 38 days to getting it done in two days. kaizen is a Japanese word meaning “change for the better,” – the process of continually improving every aspect of your business.
We taught ourselves to be lean manufacturers. We began by working with consultants and benchmarking projects that showed what other companies had done. Learning from outside our industry, we found great ideas and breakthroughs for our entire company.
Challenge Everything
We challenged our own beliefs and what we thought we could achieve. It was about working smarter, not harder. During week-long kaizen, cross-functional teams would come together to improve a specific area or process. Many employees took part in improving the layout of work areas, building fixtures, eliminating setup time, studying the ergonomics of our work, designing new tools and procedures, keeping track of what worked and what didn’t, reducing waste—we did whatever the team thought would bring improvement.
In particular, we monitored our progress in improving such things as the amount of waste scrap we generated (down in value from $350,000 to $80,000 during the past decade), the time it took to change colors in our paint booth (20 minutes down to 90 seconds), the percentage of orders we accurately fulfilled (up to 99.8 percent from 86 percent in 2000), the time it took for us to produce and deliver orders and the savings we realized in manufacturing square footage—we even measured the distance our manufacturing employees walked on the job per month (down from 3.4 miles to 1.2 miles). We dropped down to a single work shift (from three), and brought tasks in-house that we used to outsource. As we’ve made all these gains, we managed to add product lines and equipment without erecting more buildings.
Empowering Employees
Through departmental and interdepartmental brainstorming, we empowered employees to bring their ideas into the light. We totally upended our culture for the better.
For something like this to work, you’ve got to have complete commitment to the process. Sometimes you’ve got to take people out of production for a week to solve a problem. Now the kaizen approach is so inbred in our company that you couldn’t pull it out no matter how hard you tried. We graduated from using lean manufacturing to having a lean enterprise.
Good Ideas Come from Everywhere
A big part of the process was moving decision-making out of the office and into the plant. The people who do the job would find better ways to do it. Simple improvements came first, then more challenging changes. It took 18 months for us to make a pass through our plant from the front end of our manufacturing process through shipping.
Transformation through Trust
When we won the Manufacturer of the Year Award from the Manufacturing Alliance in 2004, people really wanted to know how we had accomplished our transformation. The secret is in the commitment. Our employees were promised that there would be no layoffs because of kaizen. Our employees trusted that everyone would benefit from these changes.
Now it’s part of our culture, and the notion of change for the better has become a way of life. Everyone who tours our factory senses the immense pride that employees take in the process and in their work.
And this is perhaps the biggest change we saw through kaizen—our culture. We have a team that’s committed to making Landscape Structures as good as it can be, and people who want to contribute their full share. We worked together for a common cause. Numbers are easy to measure and improve, but the soft part of a business, the culture, is harder to strengthen. And we survived hard recession years because of that culture.
A Better Landscape Structures
By empowering our employees and giving them the necessary tools, we’ve become a more efficient and consistent company, leading the industry in manufacturing, one playground at a time. These are just a few of the accomplishments we’ve achieved through our kaizen process:
- Decreased process time on the tube bender from 25 to 2 minutes
- Decreased the time it takes to change color on the paint line from 25 to 1.5 minutes
- Decreased the time to change over the break press from 15 minutes to 1 minute.
- Decreased the drill press changeover from 18 minutes down to 30 seconds.
- Decreased the TenderTuff™ color change process from 12 minutes to 4.5 minutes.